The Pantone® Matching System is the standard color matching system for the print industry. Pantone offers many different books to define colors. From spot colors to process colors, Pantone has the match that’s right for your project. Let’s get to know some of the books.
Everyone is familiar with the standard PMS solid color book. It contains over 900 spot colors on both coated and uncoated stock. These colors are often chosen when screen printing. These colors appear in both the Pantone Matching Guide, which contains perforated chips, and the Pantone Formula Guide, which comes in a fan style book for easy reference.
Pantone also categorizes process colors. The Pantone Process Guide contains over 3,000 process color combinations contained in either two binders of removable chips, or a convenient fan book. These colors are arranged chromatically and have been assigned easy referencing numbers.
Another helpful guide is the Solid to Process conversion book. It shows the closest simulated process match to Pantone’s solid colors. Some colors don’t convert as well as others, so this guide is invaluable when choosing spot colors that will be separated as process.
We recommend investing in any of these color guides. They provide an accurate color reference before the job prints and provide your printer with a way to match your colors exactly.
Pantone Solid Colors
Over 900 colors to choose from. Popular colors for screen printing. C or U after the number indicate coated or uncoated stock.
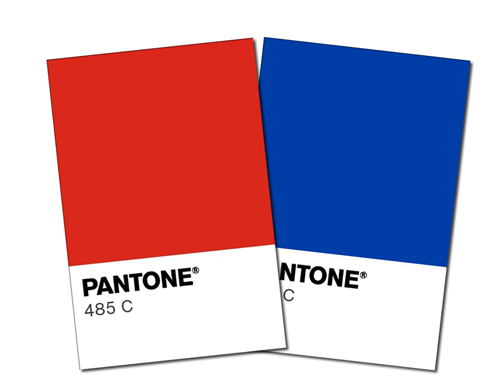
Pantone Process Colors
3,000 color mixes to choose from. The “S” stands for SWOP inks (Specifications of Web Publications). The number is the page number in the guide with the row number on the page after it.
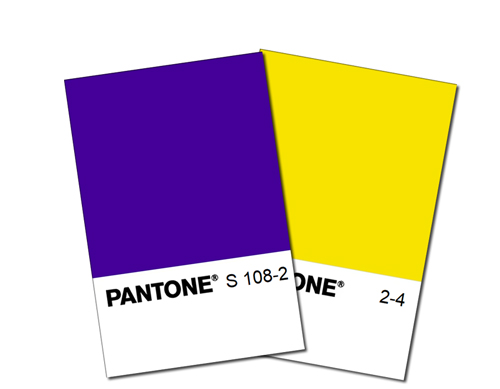
Pantone Solid to Process
Solid color side by side with its closest process equivalent. Remember, solid PMS colors don’t always convert to process as well as expected.
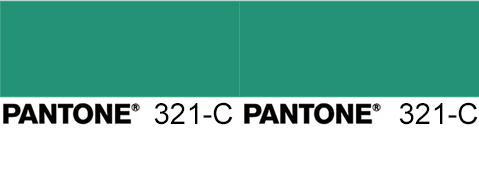